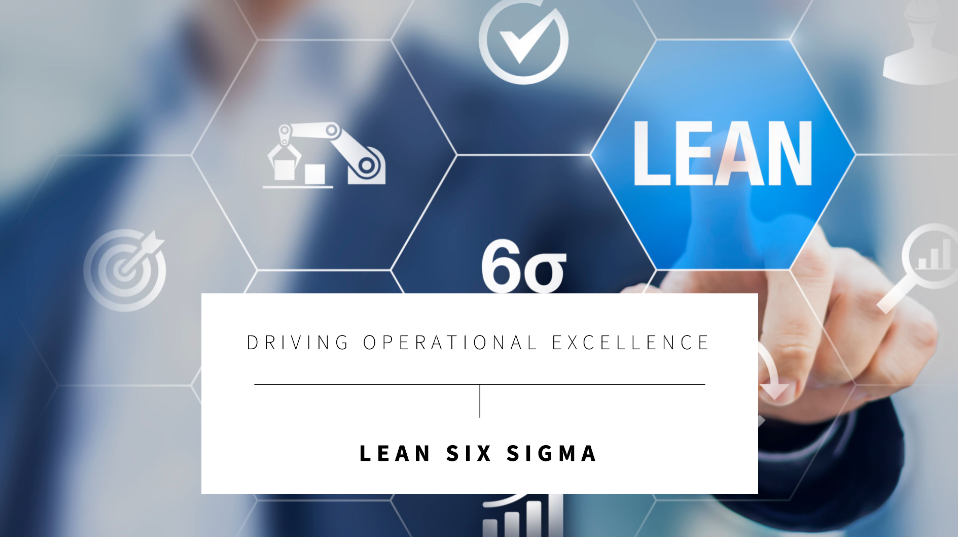
Lean Six Sigma is a powerful methodology that combines the principles of Lean manufacturing and Six Sigma to enhance organizational efficiency and quality. Lean focuses on eliminating waste and streamlining processes, while Six Sigma aims to reduce variability and defects in processes. Together, they create a holistic approach to process improvement that leads to greater customer satisfaction, increased profitability, and sustainable growth.
Key Principles of Lean Six Sigma
- Customer Focus: At the heart of Lean Six Sigma is the commitment to understanding and meeting customer needs. Organizations strive to deliver products and services that not only meet but exceed customer expectations.
- Data-Driven Decision Making: Lean Six Sigma relies heavily on data to identify problems, measure performance, and guide improvement efforts. By using statistical tools and analysis, organizations can make informed decisions that lead to better outcomes.
- Continuous Improvement: Lean Six Sigma promotes a culture of continuous improvement where organizations consistently seek ways to enhance processes, reduce waste, and increase efficiency. This involves regularly assessing performance and implementing incremental changes.
- Cross-Functional Collaboration: Successful Lean Six Sigma initiatives require collaboration across departments and teams. Engaging employees at all levels fosters a sense of ownership and empowers them to contribute to improvement efforts.
- Sustainability: Lean Six Sigma is not a one-time initiative; it aims to create sustainable change within an organization. By embedding a culture of continuous improvement, organizations can maintain high levels of performance over the long term.
Benefits of Lean Six Sigma
Implementing Lean Six Sigma can yield significant benefits for organizations, including:
- Improved Quality: By focusing on defect reduction and process variation, organizations can enhance product and service quality, leading to higher customer satisfaction.
- Increased Efficiency: Lean principles eliminate waste and streamline processes, resulting in faster turnaround times and reduced costs.
- Cost Reduction: Lean Six Sigma helps identify inefficiencies, allowing organizations to reduce operational costs and increase profitability.
- Enhanced Employee Engagement: Involving employees in improvement initiatives fosters a sense of ownership and accountability, leading to higher morale and job satisfaction.
- Stronger Competitive Advantage: Organizations that effectively implement Lean Six Sigma can respond quickly to market demands and customer needs, giving them a competitive edge.
How BTCaaS Can Help with Lean Six Sigma Implementation
BTCaaS (Business Transformation Consulting as a Service) offers expert guidance and support for organizations looking to implement Lean Six Sigma methodologies effectively. Here’s how BTCaaS can assist:
1. Assessment and Strategy Development
BTCaaS consultants begin by assessing the organization’s current processes and performance metrics. They identify areas for improvement and develop a customized Lean Six Sigma strategy that aligns with organizational goals and objectives.
2. Training and Certification
BTCaaS provides comprehensive training programs for employees at all levels. From Green Belt and Black Belt certifications to workshops on Lean principles and Six Sigma tools, BTCaaS equips employees with the knowledge and skills necessary for successful implementation.
3. Project Management Support
Implementing Lean Six Sigma involves managing multiple projects simultaneously. BTCaaS consultants help organizations prioritize projects, establish clear objectives, and allocate resources effectively. They provide ongoing support throughout the project lifecycle to ensure successful outcomes.
4. Data Analysis and Process Mapping
BTCaaS consultants leverage data analysis tools to identify root causes of issues and map existing processes. By visualizing workflows, organizations can pinpoint inefficiencies and areas for improvement, laying the groundwork for effective solutions.
5. Kaizen and Continuous Improvement Initiatives
BTCaaS promotes a culture of continuous improvement through Kaizen events—focused, short-term projects aimed at specific process enhancements. Consultants facilitate these events, guiding teams through brainstorming, analysis, and implementation phases.
6. Technology Integration
Leveraging technology is critical for Lean Six Sigma success. BTCaaS assists organizations in selecting and implementing tools that support data collection, analysis, and process improvement, enhancing overall efficiency.
7. Performance Measurement and Reporting
BTCaaS helps organizations establish key performance indicators (KPIs) to measure the impact of Lean Six Sigma initiatives. Regular reporting and analysis provide insights into progress and areas needing further improvement.
8. Sustainability and Cultural Change
Implementing Lean Six Sigma is not just about processes; it’s about changing the organizational culture. BTCaaS helps organizations embed Lean Six Sigma principles into their corporate culture, ensuring that continuous improvement becomes a core value.
Conclusion
Lean Six Sigma is a proven methodology that drives operational excellence by combining the strengths of Lean and Six Sigma principles. Organizations that embrace this approach can improve quality, enhance efficiency, and achieve sustainable growth.
BTCaaS consultants bring the expertise and experience needed to guide organizations through the Lean Six Sigma implementation journey. From assessment and training to ongoing support and performance measurement, BTCaaS provides comprehensive solutions that empower organizations to achieve their operational goals.
Partner with BTCaaS to harness the power of Lean Six Sigma and transform your processes, delivering exceptional value to your customers and stakeholders. With expert guidance and a commitment to continuous improvement, BTCaaS can help your organization achieve lasting success.